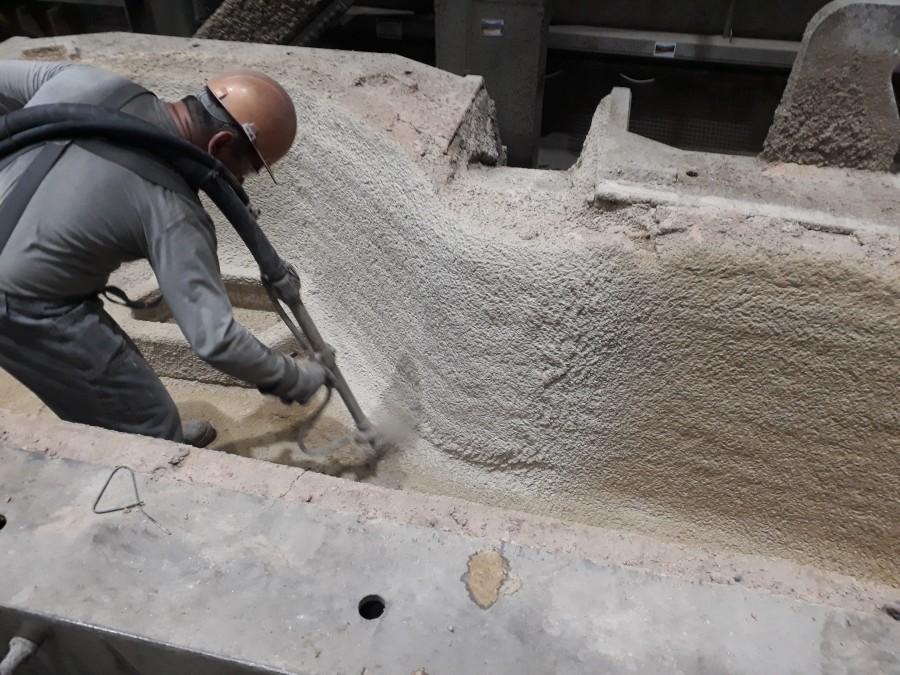
Tundish system or middle ladle is the mechanism of melt distribution from the steel ladle to continuous casting molds. The correct operation of this mechanism has a significant impact on the quality and speed of production of ingots.
The preparation of tundish for use under melting requires high skill and experience, which along with the high quality of consumable refractory materials makes the work easy and safe. Concurring to the size of the tundish, the number and time of melting from the tundish, the quality and melting temperature and other parameters that vary from one factory to another, the tundish preparation staff will discover the essential ability after a few time.
However, the following instructions have been prepared in general and can be a guide for the consumption and application of Tundish coating mix in order to reach reliable quality for melting.
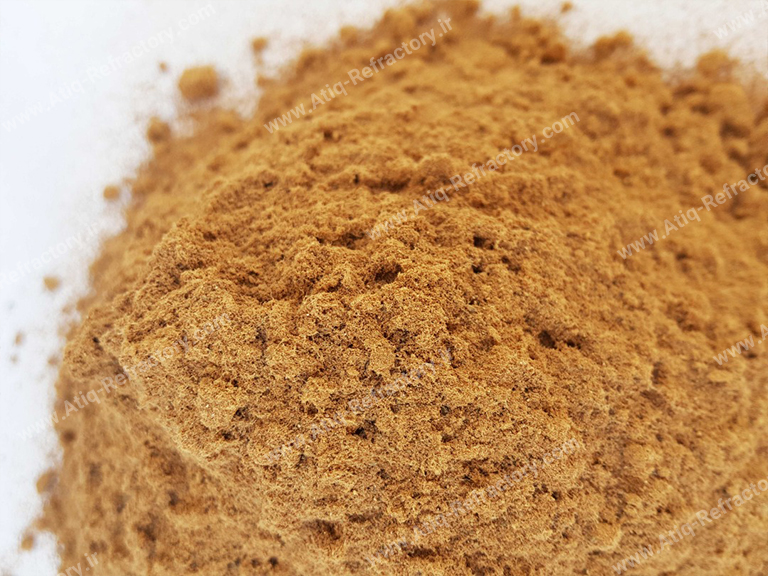
1. The prepared tundish plaster for coating should be cooled as much as possible so that it does not burn the hand. The hotness of the plaster causes the water to evaporate quickly and the work becomes difficult for the preparation staff.
2. The bottom refractory layer (alumina mix) must be lack of slag or melt sticking to the body. If this layer is worn or dull due to use, it is necessary to repair and modify it.
3. If the coating is done by troweling, the tundish plaster is mixed with about 25-30 weight percentage of water by a paddle mixer and it is ready to be drawn as mud. It is necessary to have enough moisture so that if a ball of it is placed in the hand, it does not fall from the sides of the fingers.
4. It is better to cover Tundish in two stages. At first, a layer with a diameter of about 2 cm is stretched, and after half an hour, the second layer is applied to prevent the mix from falling.
5. The most suitable diameter of the covering layer on the body of tundish is about 3-5 cm and for the floor is 6-8 cm.
6. After the entire surface and floor of the tundish is covered, it should be allowed to stand for about 2 hours without moving until the coating water is absorbed and the initial strength is obtained. Then fill the cracks created on the surface with a trowel
7. After the coating work is finished, the tundish is kept motionless for 20 to 24 hours until the mix strength is obtained.
8. After the initial drying, the tundish is transferred under the burner and the tundish is dried with gentle heat. The temperature until complete drying should not exceed 150 degrees Celsius.
9. After drying at a temperature of 150 degrees Celsius, the tundish is heated for at least four hours at a temperature between 500-700 degrees Celsius.
In the last step, the temperature of the stretched plaster should be brought to 1000 degrees centigrade in at least three hours with a gentle slope and without cooling the plaster, and then the melting operation is done.
11. If it is not possible to dry in the above step, before the melting stage, the tundish should be brought from the ambient temperature to a temperature above 1000 degrees in a period of about 4-5 hours with a gentle slope, and then the melting operation is done.
12. It should be noted that after the last stage of drying and before casting, the plaster should not be cooled.